This morning, I saw a great question pop up on LinkedIn from KP Reddy:

It’s a thought-provoking question which reminded me of the concept of McDonaldization, a term coined by sociologist George Ritzer. This is something that I learned about in high school and it has stuck with me ever since. It describes how industries optimize for efficiency, predictability, uniformity, and control, just like McDonald’s perfected its assembly line for fast food. But this principle doesn’t just apply to burgers, it’s the secret behind how companies like Target, Walmart, and Wegmans scale their physical spaces to thousands of locations across the country.
In the world of construction and procurement, the best way to achieve this level of standardization and efficiency is through Owner-Furnished, Contractor-Installed (OFCI) items. By giving owners full control over critical assets, businesses can reduce costs, streamline procurement, and ensure consistency across every project. But what happens when projects don’t follow this approach? Chaos. Imagine if every McDonald’s location let designers pick their own furniture and kitchen equipment—it would be a logistical nightmare.
Let’s break it down.
1. Standardization & Compliance: The Secret Sauce
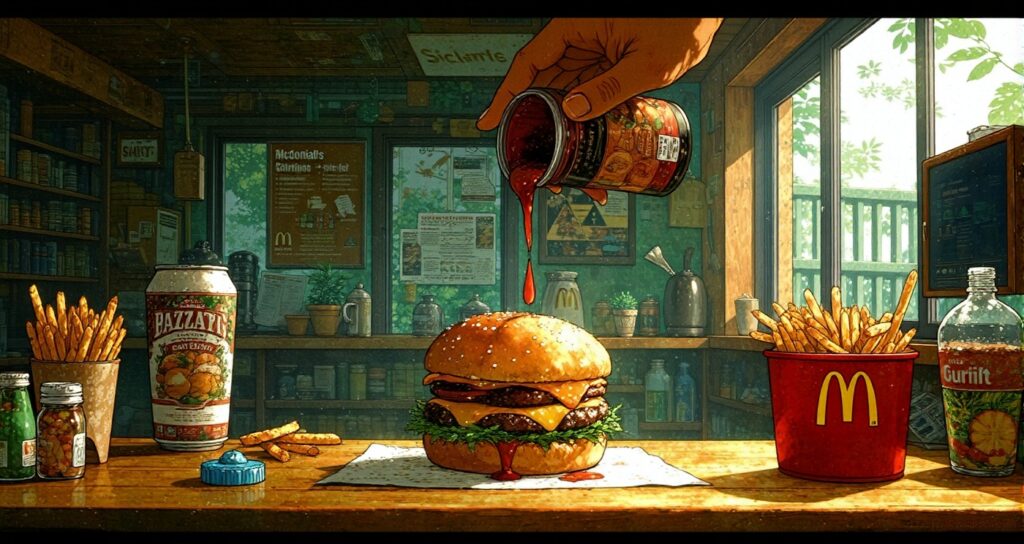
Just like a Big Mac tastes the same in Manila as it does in Los Angeles, physical spaces need to maintain design consistency across locations. OFCI ensures that furniture, fixtures, and equipment (FF&E) align with brand standards, regulatory requirements, and operational needs. When design teams specify their own products per project, it creates inconsistencies that make future maintenance and renovations a mess.
Imagine if McDonald’s let every franchise and/or their respective architects choose its own kitchen layout… One store might have deep fryers in the front, another in the back, and none of them would operate the same way. The same principle applies to retail spaces: consistency reduces friction and ensures every location meets the same quality standards.
In addition, each restaurant would spend countless hours selecting the kitchen equipment. This may seem like a simple trip to the appliance store, but if you’ve ever designed a commercial kitchen, you know how much work actually goes into it.
By centralizing asset decisions, owners create a repeatable, scalable playbook that maintains brand integrity and speeds up approvals.
2. Cost Savings: Cutting Out the Middleman (and the Extra Costs)
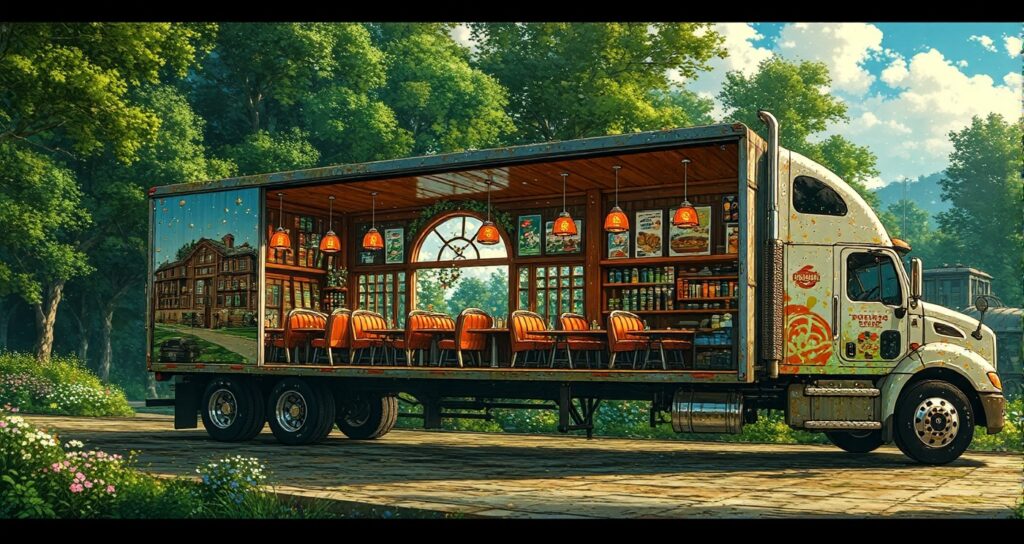
McDonald’s can sell a burger for a few bucks because it buys ingredients in bulk, cutting out inefficiencies. The same logic applies to OFCI procurement. When owners take control of purchasing, they reduce contractor markups, minimize unnecessary customization, and leverage bulk pricing across multiple locations.
A study on public works projects found that direct procurement reduces costs by up to 10% by cutting out middlemen and supplier markups (source). Now, scale that savings across hundreds or thousands of locations, and the numbers become impossible to ignore.
If every McDonald’s location sourced its own potatoes from different vendors instead of McDonald’s corporate handling it, costs would skyrocket, quality would suffer, and supply chain delays would become unavoidable. The same thing happens in retail construction when every project team sources assets independently. OFCI eliminates this waste and creates massive savings.
3. Scalability: The Assembly Line of Construction
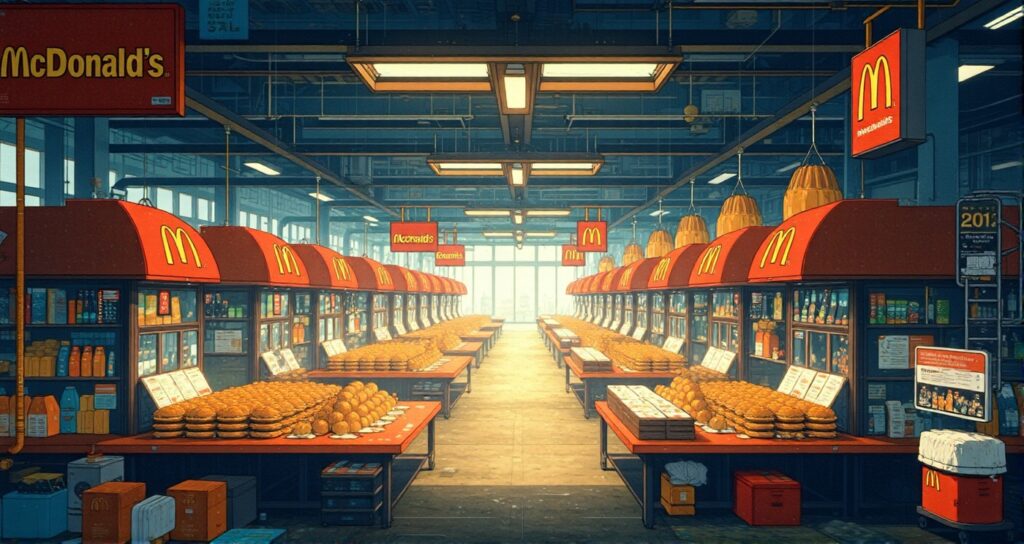
McDonaldization isn’t just about saving money, it’s about scaling efficiently. McDonald’s doesn’t reinvent its kitchen setup for every new location; it follows a precise, repeatable formula that makes expansion fast and cost-effective. That’s exactly what OFCI does for commercial spaces.
When procurement is centralized, scaling new locations becomes a copy-paste operation instead of an unpredictable mess. Construction teams get exactly what they need, procurement timelines shrink, and store openings happen on schedule.
Compare that to a world where every project selects different assets and suppliers… It’s slow, expensive, and full of unnecessary delays. According to industry research, 80% to 90% of construction projects experience budget overruns or delays, often due to procurement inefficiencies (source). With OFCI, businesses cut through the complexity and keep projects moving.
Final Takeaway: The McDonald’s Model Works for Repeatable Design Too
The same principles that allow McDonald’s to serve billions of customers apply to construction and asset management. Standardization, cost control, and scalability create repeatable, efficient processes that drive success.
When businesses embrace OFCI, they take control of procurement, eliminate inefficiencies, and create a playbook for expansion; just like McDonald’s did for fast food. Whether you’re rolling out a hundred new stores or upgrading existing locations, this model ensures every site meets the same standards, at the lowest cost, and on time.
It’s time to stop treating asset procurement like a custom-built menu and start thinking like McDonald’s. OFCI is the key to scaling smarter.
Ephany provides a central platform to successfully manage OFCI FF&E processes. Ask me how!