I believe BIM is experiencing some growing pains, as with any new technology would. I’m starting to see that there is too much data in models, particularly regarding assets such as the furniture, fixtures, and equipment (FF&E).
I do agree that any data that is required for design and construction processes need to be included in the model, especially the information that is shown on the permit and construction drawings. However, in the context of owner furnished items (OFI) for repeatable commercial real estate projects, storing too much asset information within BIM models can lead to inefficiencies, higher costs, and unnecessary complexities. Here’s why.
1. Asset data gets locked away in a model.
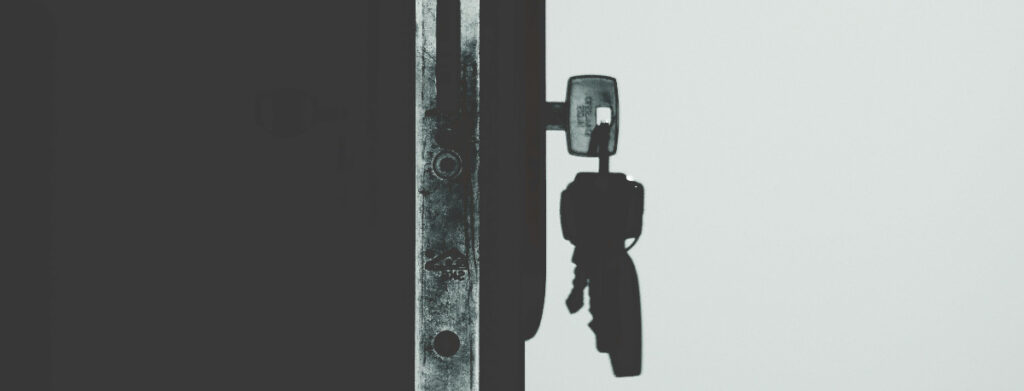
One of the most significant drawbacks of storing asset data in BIM models (e.g., data within in a Revit model) is that access to these models is restricted. Only team members with specialized knowledge of BIM tools and the appropriate licenses can manage the data directly.
Therefore, modifying that data in a Revit file isn’t as simple as editing a cell in a spreadsheet. Every update requires careful attention to ensure the integrity of the model, which often involves editing complex Revit Families. Additionally, these updates are often left up to the BIM team because the project-level teams are not permitted to make changes to program-wide standards.
2. Updating Asset Data in BIM is Expensive
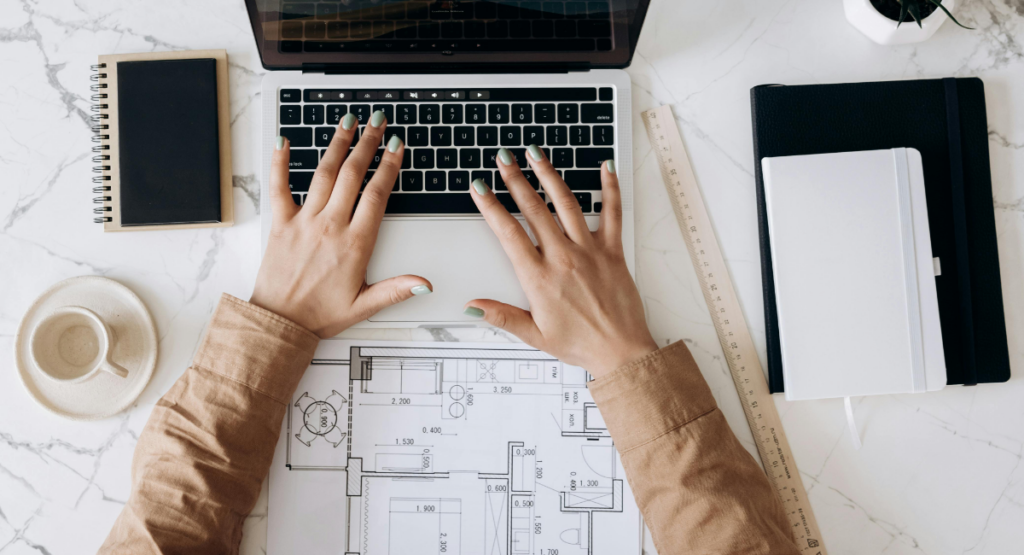
Let’s think about a scenario where a Revit Family contains incorrect information about a particular furniture, fixture, or equipment (FF&E). For an owner-furnished item (OFI), the update needs to be made available to the project teams. Sometimes this can come in the form of a formal design bulletin, but for owners who have their own BIM manage, a Revit Family first needs to be manually updated by a BIM manager. Either way, this change needs to be off to the project teams to update within their project models.
For programs with repeatable design, that means rolling out the updated Revit Family to an entire fleet of stores. This process is not only time-consuming for that broader teams and their consultants, but will have downstream impacts on any project which includes the asset (which means added project costs).
The cost of updating Revit Family data.
For most organizations executing thousands of projects, making updates often requires engaging with an architectural firm in which the cost can range from $150 to $200 per hour (or more). Sure, an update to a Revit Family for $150 on a single project, is peanuts, however, now consider the scale of large programs—such as retail chains with thousands of locations—these costs quickly add up.
Think about our earlier example of an entire fleet of retail stores that need an updated Revit Family. Let’s assume the update takes three hours and needs to be applied to 1,000 projects.
$600 in fees x 1,000 projects = $600,000
That’s only for the design work. If drawings need to be resubmitted to the owner or contractor, this cost could easily double or triple.
3. Project Delays Equate to Losses in Revenue.
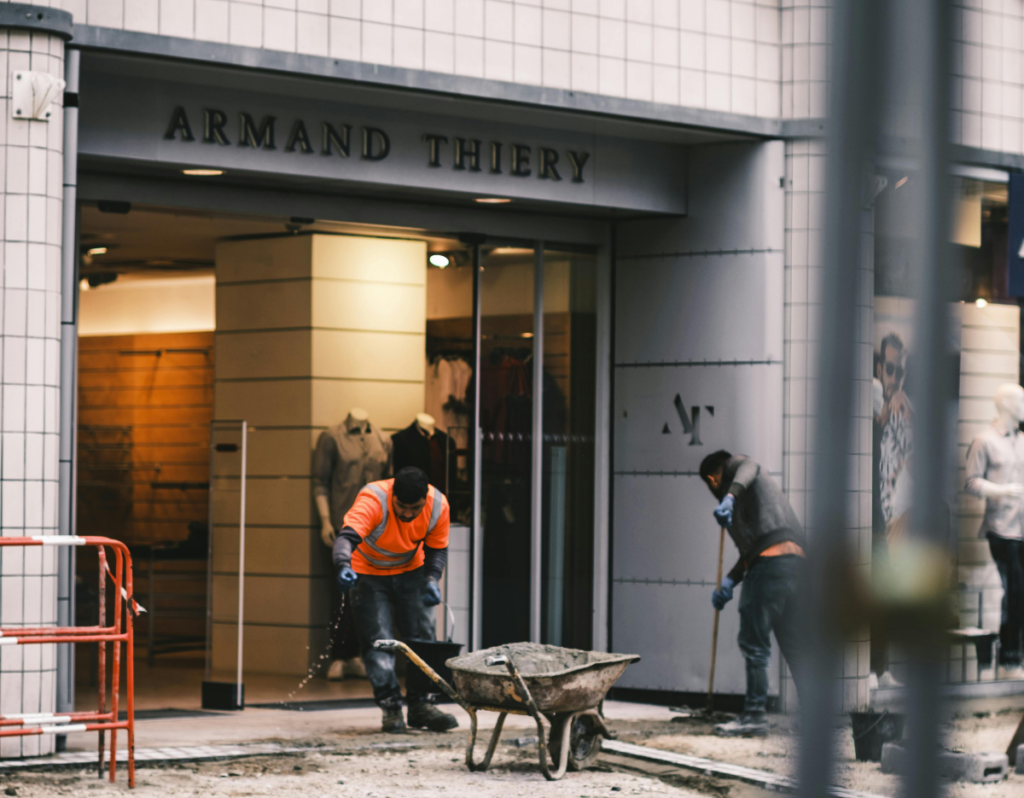
Moreover, these updates can delay projects, as firms may take days or weeks to complete the requested changes, further increasing both direct and indirect costs.
If a required update to asset data within a BIM model causes delays to a construction schedule, it could impact the launch date of a project, which would undoubtedly result in losses in revenue. According to Wave Grocery, large format stores could lose an average of $623,000 per week that a store launch is delayed.
The Case for a Better Approach
While BIM models are invaluable for design and construction coordination, relying on them as the primary source of asset data creates unnecessary limitations.
Asset data—such as product specifications, procurement information, facilities management history—needs to be easily accessible and editable for all team members involved in a project.
A Smarter Alternative
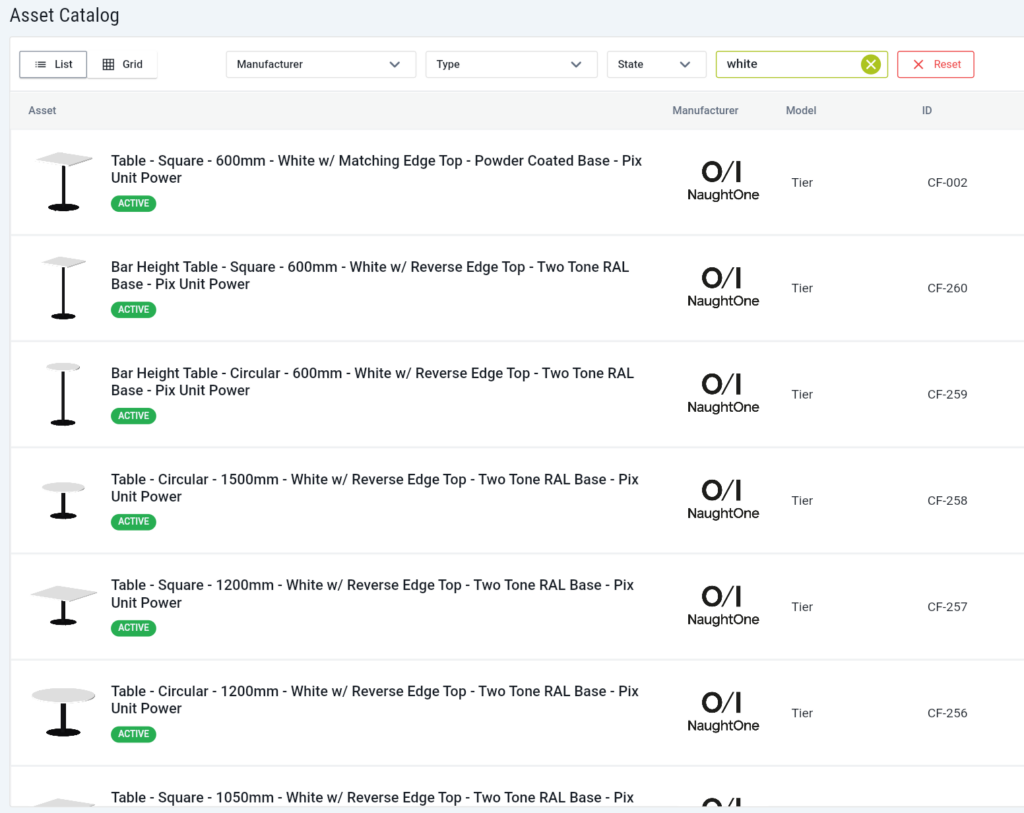
By separating asset data from the BIM model and using a centralized platform like Ephany, teams can overcome these challenges:
1. Ease of Updates
With OFI asset data stored in a system accessible to all relevant stakeholders, it can be easily updated regardless of their technical expertise. In addition, the data can simply be modified on a platform which doesn’t impact the design and construction models which means changes can be made quickly, without the need for complicated software or expertise.
2. Cost Efficiency
By reducing asset data that does not need to be published in drawings, you alleviate some dependency on architectural firms or specially trained BIM specialists. As described earlier, this can save a large organization millions of dollars annually.
3. Seamless Integration
Data can still connect back to BIM models through unique asset IDs, ensuring consistency without the need to lock it into the model itself. Ideally, you would implement a platform such as Ephany, which offers connectors to popular BIM and construction management tools. This way, you can maintain synchronization with the assets as shown in BIM models and construction drawings as needed when it’s time to calculate a bill of materials (BOM) or other analysis.
Conclusion
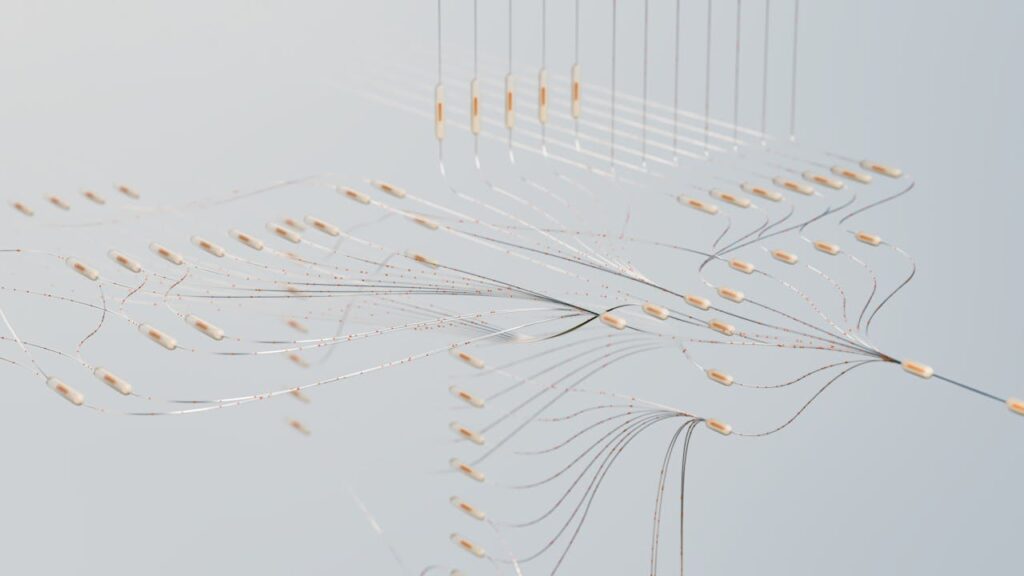
Storing asset data exclusively within BIM models creates barriers that lead to inefficiencies, high costs, and bottlenecks. By moving this data into a centralized platform that integrates with (not relies on) BIM processes, teams can streamline workflows, reduce costs, and ensure everyone has access to the information they need.
If you’re managing large-scale retail or commercial projects, it’s time to rethink how you handle asset data. Let’s talk about how Ephany can help you simplify your processes and avoid the pitfalls of BIM-centric asset management.