Building out physical retail stores is a high-stakes game—one where a single misstep can cost thousands (or even millions). Have you ever had a store opening delayed because the wrong fixtures arrived? Or watched in horror as a brand-new display case was installed upside down? You’re not alone. Mistakes in procurement, installation, and project management can quickly turn a well-planned rollout into a financial nightmare. The good news? These costly issues are avoidable.
In this article, we’ll break down the biggest money pits in retail construction—inefficient procurement, supply chain mishaps, installation blunders, and budget overruns—and, more importantly, how to prevent them. Read on to find out how better planning, smart project management, and a little foresight can keep your FF&E costs under control and your store openings on schedule.
1. Inefficient Procurement Processes
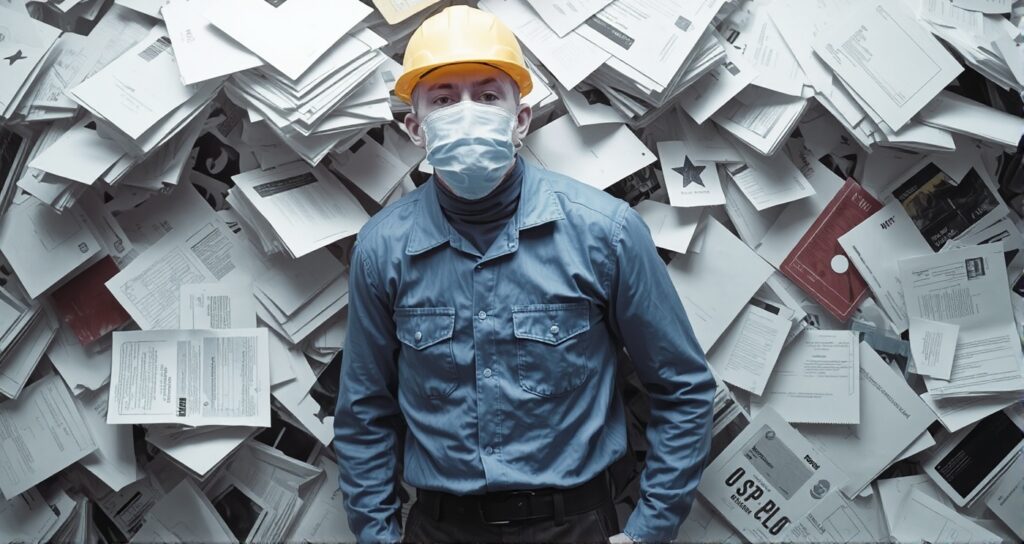
Disorganized or ad-hoc procurement of FF&E can lead to higher prices, inconsistent quality, and delays. Lack of centralized purchasing and poor vendor management mean retailers miss out on bulk discounts and reliable delivery schedules.
Centralized procurement can improve efficiency by up to 30% in multi-location operations, and long-term vendor partnerships can cut costs by ~20% through negotiated pricing (source).
Retailers without these strategies often face overbudget spending and late deliveries. For example, not standardizing FF&E specs or consolidating orders across stores can result in variability in pricing and quality, as well as rush orders that incur premium shipping fees.
Reduce Procurement Inefficiencies in Three Ways
- Standardize FF&E for designs across projects (ensures consistency and bulk leverage).
- Centralize procurement and negotiate volume deals with vetted vendors (captures economies of scale and better terms).
- Leverage technology for procurement – e.g. ERP or procurement platforms – to track orders and budgets. Digital procurement tools have been shown to reduce costs by ~10% while improving transparency (source).
Ephany streamlines the way your team manages FF&E procurement by giving you complete visibility into assets, their components, and sourcing details—all in one place. Instead of scrambling to track fixture parts, distributor options, pricing variations, and shifting lead times across spreadsheets, Ephany centralizes this data, ensuring your team always has accurate and up-to-date information. With the ability to generate a detailed bill of materials (BOM) in just a few clicks, you get a clear, real-time picture of costs and availability, helping you make informed decisions, prevent budget overruns, and keep projects on schedule.
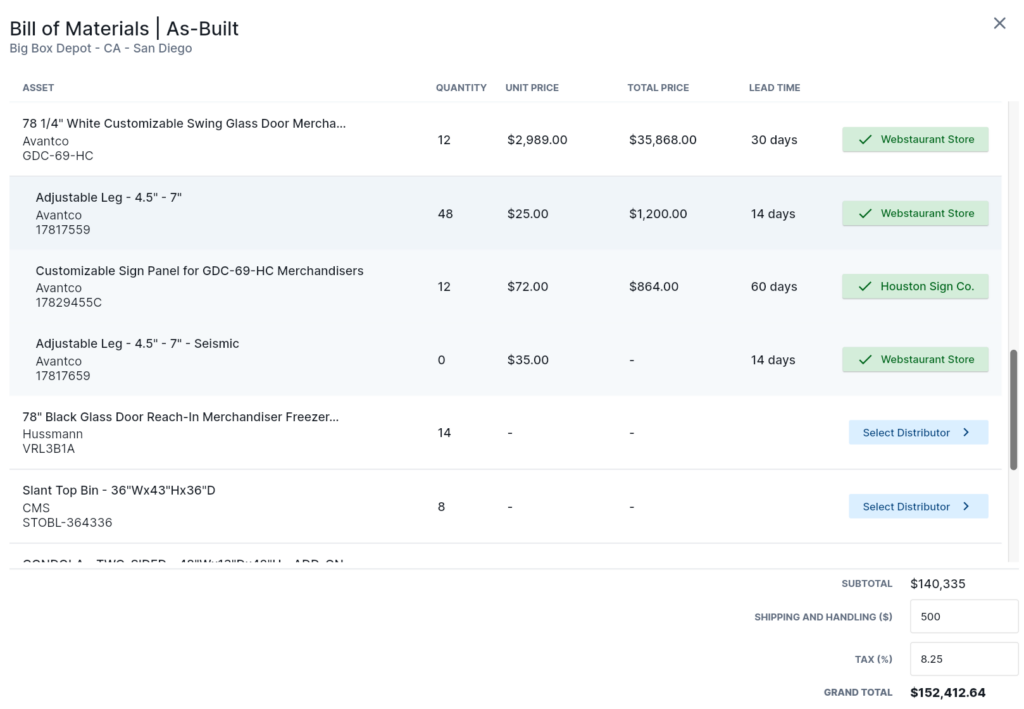
2. Installation Errors
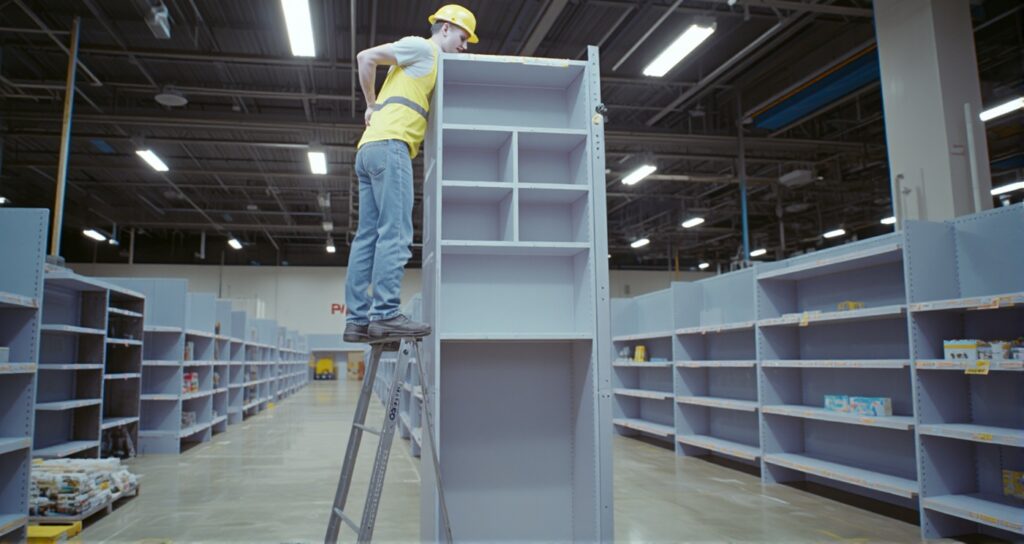
Poor workmanship or rushed installation of fixtures and equipment can trigger costly rework and repairs. Mistakes like misaligned shelving, improper electrical hookup of equipment, or installing items in the wrong sequence can damage assets and require do-overs.
Studies show that construction rework (i.e., redoing work due to errors or changes) typically eats up about 5–9% of a project’s cost (source). In the U.S. alone, rework accounted for an estimated $65 billion (5% of total construction spending) in 2020 (source).
Best Practices to Avoid Installation Errors and Rework
Clear, accessible documentation is essential for ensuring FF&E installations are done right the first time. Without the right specifications and guidelines, contractors risk costly mistakes, delays, and rework. Investing in document control not only streamlines installation but also helps maintain consistency across multiple locations.
Ephany makes this effortless by providing a centralized hub for all FF&E documentation. Teams can store and organize PDFs, CAD files (DWG), and BIM models—including Revit families—directly within the asset catalog. This ensures that contractors and project teams always have the latest, most accurate information at their fingertips, reducing errors and keeping installations on track. No more hunting through emails or outdated files—just seamless access to the data you need, exactly when you need it.
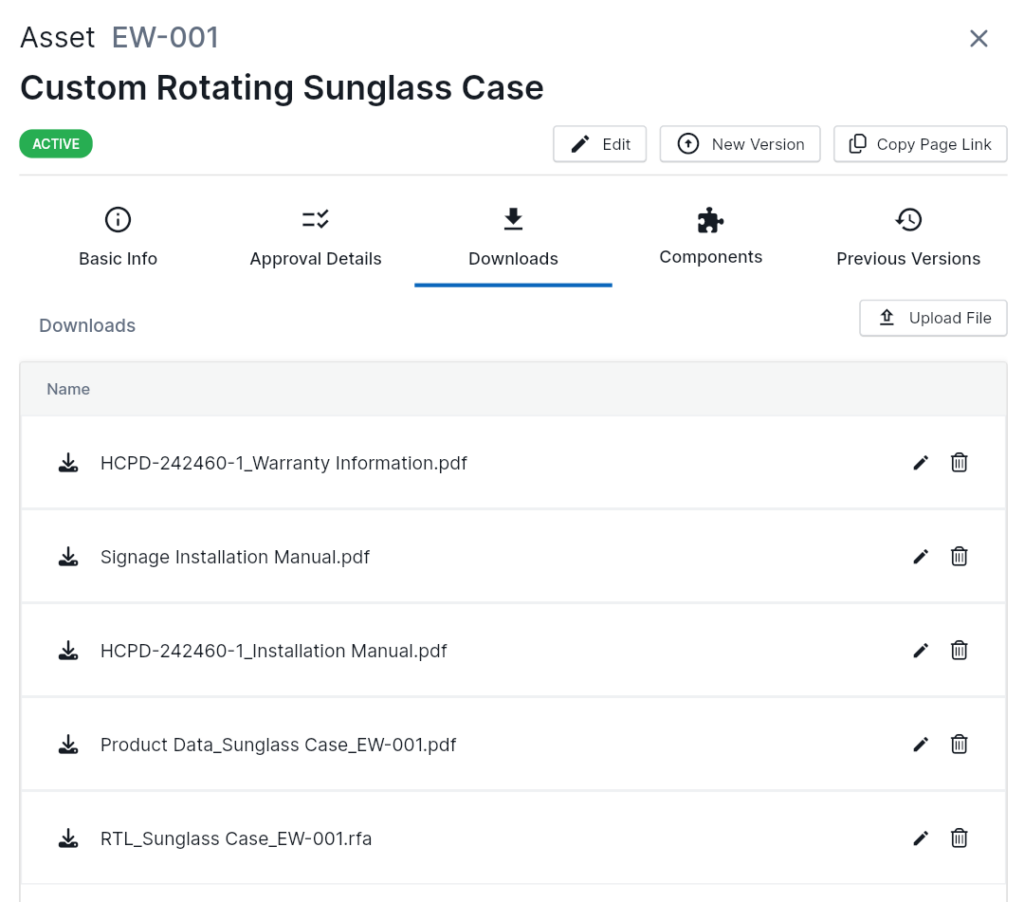
3. Supply Chain Disruptions

Global supply chain issues can wreak havoc on retail construction projects. Volatile material costs and long lead times for FF&E have been a major driver of cost overruns and delays in recent years. For example, construction input costs surged ~17% in 2022 (far above general inflation), with core materials like steel up 124% and lumber up 61% since 2020 (source).
One national retailer saw its average per-store buildout cost jump from $400–500k to $700k due to these rising prices. Such increases at 40–75% per store forced that company to pause expansion to redesign for cheaper materials – an illustration of how supply-chain-driven cost spikes directly hit the bottom line.
Beyond cost, delayed shipments of critical FF&E can postpone store openings (leading to lost sales opportunities).
In a 2022 industry survey, up to 25% of material deliveries to construction sites were late or incomplete, underscoring the unpredictability of supply chains (source).
For retailers, a delay into the next quarter or missing the holiday season can be devastating, since the holiday period can account for a majority of annual sales for some brands (source). In short, supply chain disruptions often translate to schedule overruns (projects delivered late) and necessitate expensive workarounds or last-minute substitutions.
Mitigation Strategies for Supply Chain Disruptions
Relying on a single supplier can be a major risk—delays, price fluctuations, or inventory shortages can throw an entire project off schedule. Diversifying vendors and having backup options for critical fixtures helps retailers stay agile when supply chain disruptions arise. Real-time tracking of lead times and proactive coordination with suppliers can prevent last-minute surprises and costly delays.
Ephany makes supplier management seamless by allowing teams to compare multiple distributors for the same asset, ensuring lead times and pricing align with project requirements. For even greater accuracy, suppliers can be invited to collaborate within Ephany, updating lead times and availability directly. This keeps procurement teams working with the most up-to-date information, reducing delays and keeping projects on track—without the back-and-forth of endless emails and phone calls.

Conclusion: Keeping Track of FF&E Properly Helps Ensure a Successful Store Launch
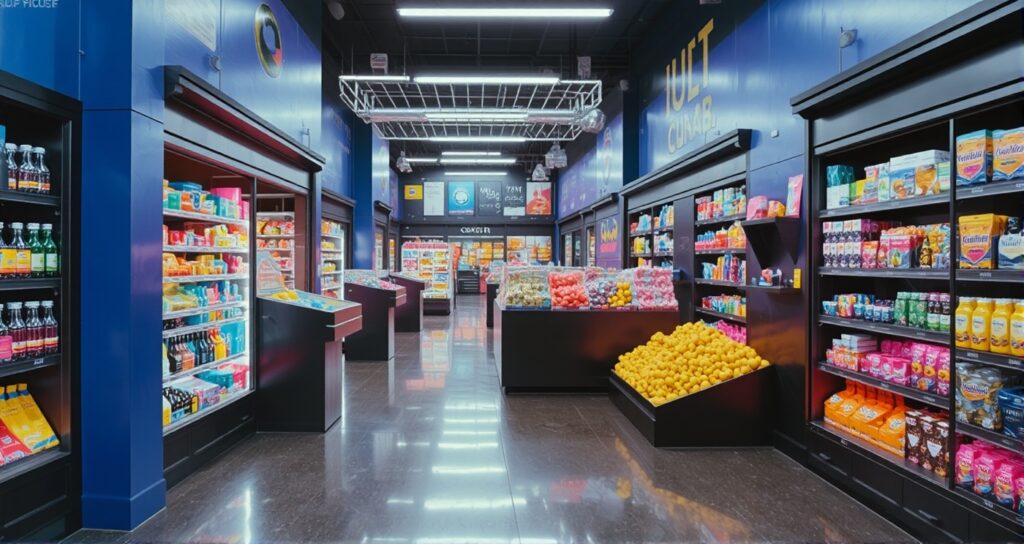
Inefficient procurement, installation errors, and supply chain disruptions can quickly turn a well-planned retail build-out into a costly, time-consuming challenge. But with the right strategies—centralized procurement, quality-focused installation, and proactive supply chain management—retailers can stay ahead of these risks and keep projects on track.
Ephany makes this even easier by giving your team the tools to manage every aspect of FF&E with clarity and control. From tracking assets and suppliers to streamlining approvals and ensuring real-time access to critical documents, Ephany helps retailers simplify the complexities of multi-site projects—so stores open on time, on budget, and exactly as planned.
However, these aren’t the only pitfalls that can derail a retail construction project. In the next section, we’ll dive into even more budget-draining problems—cost overruns, poor project management, and damages & rework—and explore how to prevent them before they take a toll on your bottom line. Stay tuned!
About the Author
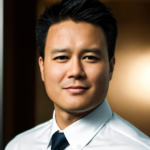
- Jay is a seasoned BIM manager with over 20 years of experience across design and construction firms. Most recently as Sr. BIM Manager at Amazon, he focused on establishing processes and standards to simplify furniture, fixture, and equipment (FF&E) asset management for repeatable design (physical retail).
Latest entries
Industry KnowledgeMarch 13, 2025Common Issues with Retail FF&E and How to Mitigate Them – Part One
Industry KnowledgeMarch 1, 2025McDonaldization and Construction: How Owner-Furnished Items Unlock Scalability
Industry KnowledgeFebruary 10, 2025Decluttering Your Data: Why AI Alone Won’t Solve the Mess
Industry KnowledgeJanuary 28, 2025Lean Out Your BIM Processes by Reducing Asset Information in Your Models